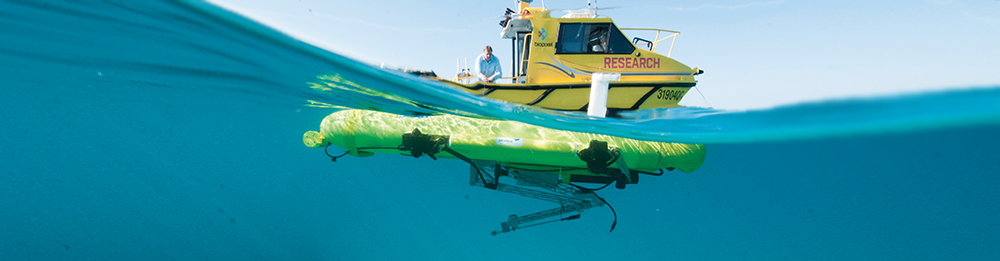
Sustainability: new materials and fabrication schemes, physical systems development, power and energy
Robots currently consist of gears, motors, and electromechanical actuators, but advances in new materials and manufacturing and construction techniques are changing the way that robots are built. Prototypes of new generation robots are increasingly power-efficient, multifunctional, compliant (to standards), and display biological features [SM18]. Widespread application of new materials and manufacturing techniques requires improved portable energy storage and harvesting, new materials with tuneable properties, and new fabrication strategies for these functional materials with the aim of eventually building robots that can build and repair themselves [SM18].
As the properties of new materials become better understood, it is possible to design entirely new robots. Some new materials combine both sensing and actuation, while robot designs are increasingly mimicking biological systems. Drawing inspiration from invertebrates, robots can be reimagined using a wide range of material properties (from soft tissue to bone) allowing seamless integration of dissimilar material properties, allowing distributed function, and reducing the need for complex assembly [SM18].
Multifunctional materials can increase the efficiency of robot design and simultaneously offer distributed networks of hierarchically structured sensors and actuators. The use of folding-based metamaterials (with tuneable electromagnetic or mechanical properties), multiphase composites (with simultaneous fluidic actuation or sensing), and textiles (embedded with electrical functionality) is yet to be fully explored, as is the biodegradability and recycling potential of robot-building materials [SM18]. In the future, it is envisaged that artificial muscles may replace electric motors and gears as they are lighter, quieter, and have fast reaction times. Robots would also benefit from more energy-efficient perception inspired by biological processes. Digital computers are massive and energy intensive compared to the human brain, which is compact, powerful, energy-efficient, weighs just 1.5 kilograms and consumes around 20 watts. Computer chips and the boards on which they are mounted are 2-dimensional whereas our brains comprise highly interconnected 3-dimensional circuits [AAS18].
Fabrication and assembly is typically a serial process that is slow and difficult to scale to very large or very small scales, until the discovery of synthetic molecular machines [SM18]. These molecular machines have the potential to develop hierarchical materials. These can be used to enhance the function of robots by converging additive and subtractive methods of manufacture, with emerging technologies to generate new architectures. The current robotic frontier is the use of alternative methods of fabrication that combine techniques from micro-/nanoscale (e.g., surface and bulk micromachining, physical and chemical deposition, and microscale moulding, stamping, and functionalisation used in soft lithography), mesoscale (e.g., layering and lamination common in multilayer printed circuit boards), to macroscale (e.g., multi-axis subtractive methods).
Biological systems have an amazing ability to heal or accommodate damage which is desperately required in engineered systems that otherwise rely on redundancy to cope with catastrophic failures induced by damage [AAS18]. The ability of robots to self-maintain and self-repair in harsh environments over long time periods will be a critical factor in the successful automation of many tasks. The development of multiscalar materials able to adapt and heal over time, may help robots achieve the complexity found in natural systems [SM18].
Many of the desired applications for future robots will be in inhospitable environments without access to recharging stations, so reducing energy demand, improving efficiency, and increasing energy density of storage will be extremely important [AAS18]. The operational longevity of mobile robots is typically constrained by battery power, size, and weight. These may be in the form of compact, stable, high-energy density batteries for robots working in challenging conditions and/or extreme environments [SM18]. New battery technologies for robots are being developed that are safe and affordable, with longer cycle lives, robust temperature tolerance, higher energy densities, and relatively low weight. New areas of research include the use of: fuel cells, supercapacitors, silicon anodes with smart electrodes, new electrode designs for achieving enhanced capacities, and metal-oxygen, lithium-sulfur, aluminum-ion, and sodium-ion batteries. Advanced battery systems based on solid electrolytes, and flow-based, lithium-ion, lithium-sulfur, and lithium-organic batteries are also promising areas of study [SM18]. No battery can yet match the metabolic energy generation in organisms. Biohybrid robots with on-board generation or ‘foraging’ behaviours remain a research frontier [AAS18].
Energy-harvesting and storage techniques are potential solutions to the power and energy challenges facing robots. Such techniques include electromagnetic and electrostatic generators, as well as piezoelectric nanogenerators and triboelectric nanogenerators, and the use of bidirectional transducers (that allow sensors and actuators to behave as materials for energy harvesting or storage). Improving battery energy density and cost will require radical breakthroughs. While robots can ‘forage’ for energy by docking with stations where power is available or generated, and automatically recharge or upload data, no real-world systems have yet demonstrated these capabilities [AAS18]. As important as energy harvesting is, reducing robot demand for energy is achievable by implementing energy-efficient motion and perception algorithms. In the next decade, energy harvesting and storage techniques may be solved for robotics due to the strong drive for these technologies from other industries, such as the solar power and hybrid car industries. However, reducing the power and energy requirements of robots by clever adaptation of motion and perception algorithms is of equal importance.
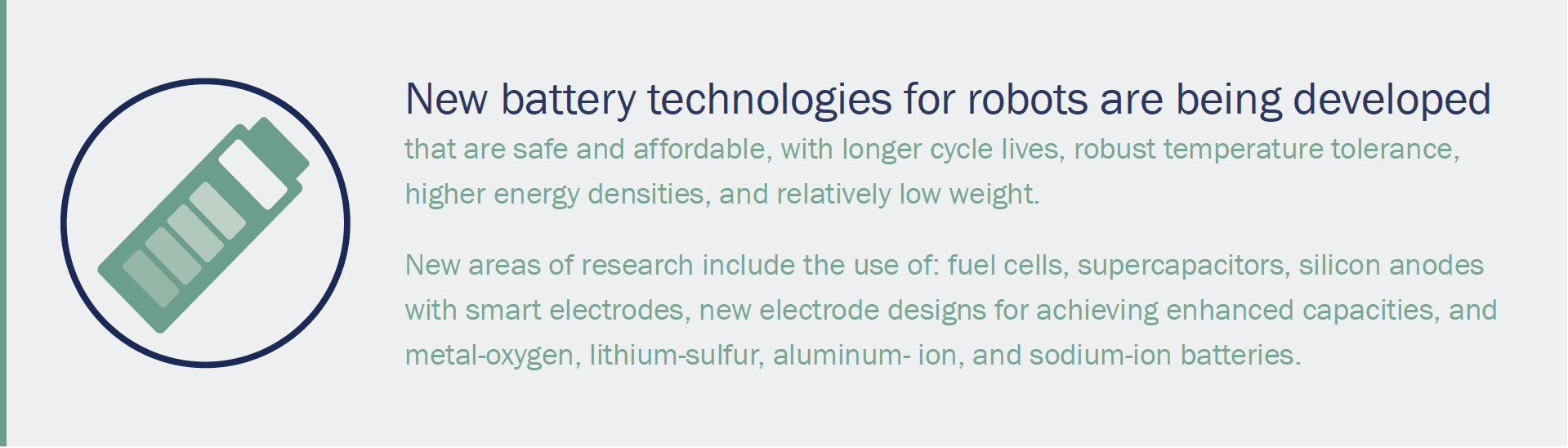