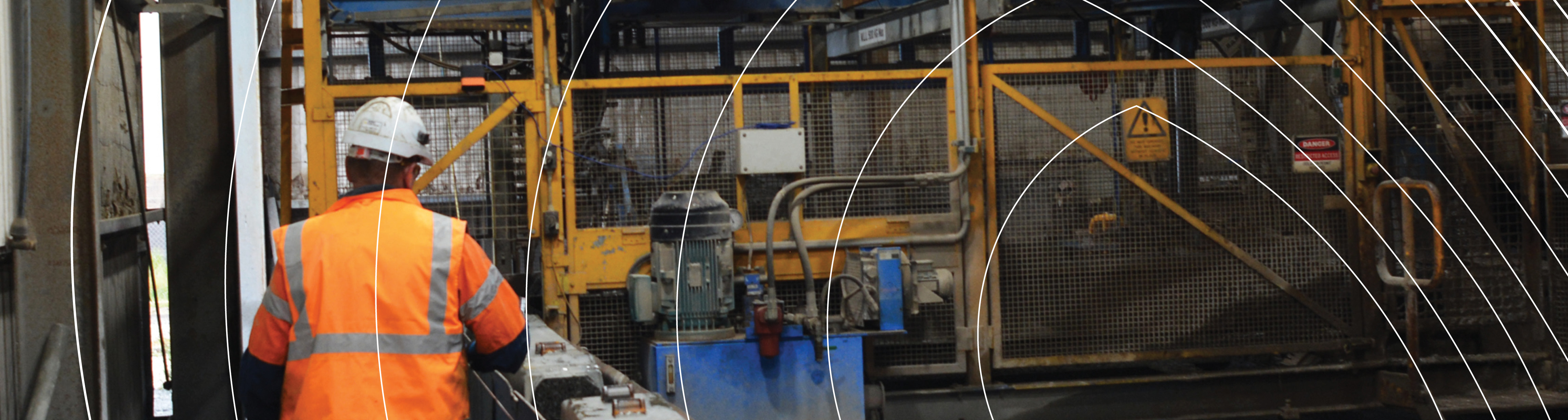
CASE STUDY: Laing O’Rourke – lifting frontline job satisfaction
Case Studies
Boeing Australia – Where humans and automation work together
Since the 2008 establishment of Boeing’s advanced research and development unit …
IR4 – Mass communication via robotic automation
IR4 is an early revenue technology company that is setting global benchmarks in …
Kalmar – AutoStrad Terminal Solution
Within the next 10-15 years many of the major stevedores will automate and the …
Wide area surveillance of the oceans requires a diversity of solutions …
Rio Tinto’s fleet of autonomous haul trucks have moved more than 1 billion tonnes of …
Share this story
Laing O’Rourke is a $AU6 billion international operation with 50 years of involvement in Australian construction and infrastructure. It prides itself on advancing off-site construction and, as a result, has embraced many fundamental manufacturing principles, as well as establishing significant scale manufacturing plants. “Our perspective is that construction is the epitome of mass-customisation – we manufacture very large scale, expensive, intricate, and complex one-off units which some call buildings,” Laing O’Rourke explains.
This philosophy is more than words. In 2011, Laing O’Rourke established a well-funded futures innovation group; the Engineering Excellence Group (EnExG) in Sydney, Australia to research, develop, deliver, and strive to lead innovations in the sector while also aiming to disrupt the industry.
One focus area for EnExG has been on exploring the deep-integration of robotics systems and capabilities into frontline work flows, environments, and machines of Laing O’Rourke operations. Recently, this workforce-need centred approach was applied to its Austrak rail sector manufacturing facility.
The result is a robot with sensing and perception capabilities that sees, understands, assesses and identifies potential issues such as manufacturing faults, needs for rework or rejection, forthcoming safety incidents, or a gambit of line issues (see picture). This creates the possibility for manufacturing machines and lines to intelligently act without worker involvement and present viable units, along with inherent recommendations to frontline workers. The disembodied robot seamlessly contributes to and is welcomed by the team.
With the line configured in this way, frontline workers are freed from the burden of routine work and can focus their expertise where they will contribute most.
Although this type of robotics implementation is notoriously difficult to measure with tangibles over a short time frame, the lift in frontline job satisfaction, engagement, and performance, along with the increased flexibility of these lines, is a demonstrable step towards operations of the future. If the robot is performing well and operations run smoothly and without incident it can, however, create the paradox of measuring the absence of negatives.
Trending Article
Working with robotics technology to improve safety, reliability and efficiency in high-risk and remote environments
Woodside is an Australian oil and gas company with a global presence, recognised for its world-class capabilities – as an explorer, a developer, a producer and a supplier of energy…
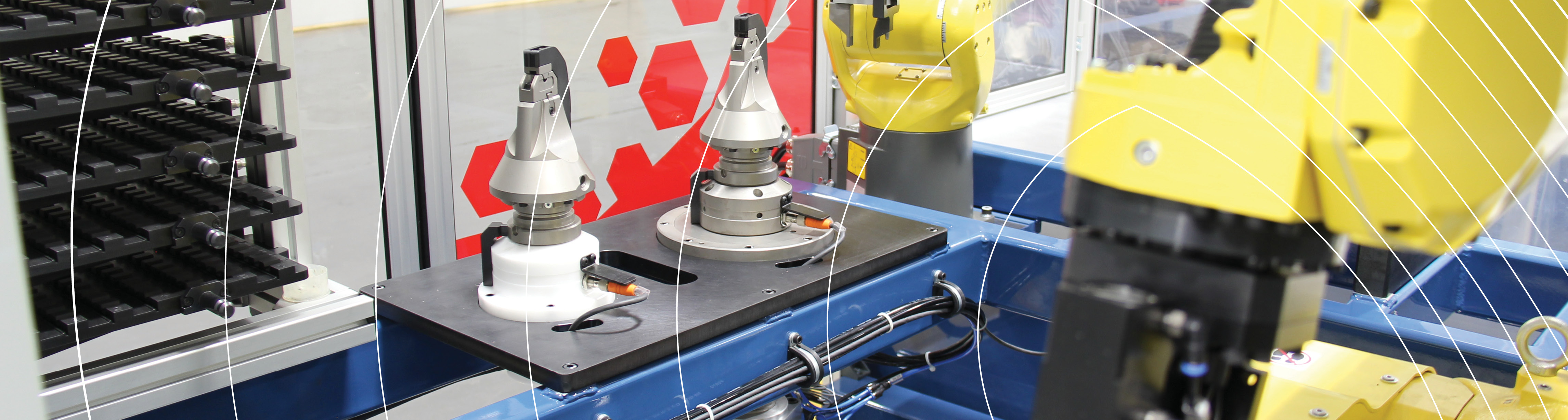
ANCA – Australia’s largest user of industrial robots
ANCA is an Australian company, founded in Melbourne in 1974, now with offices...
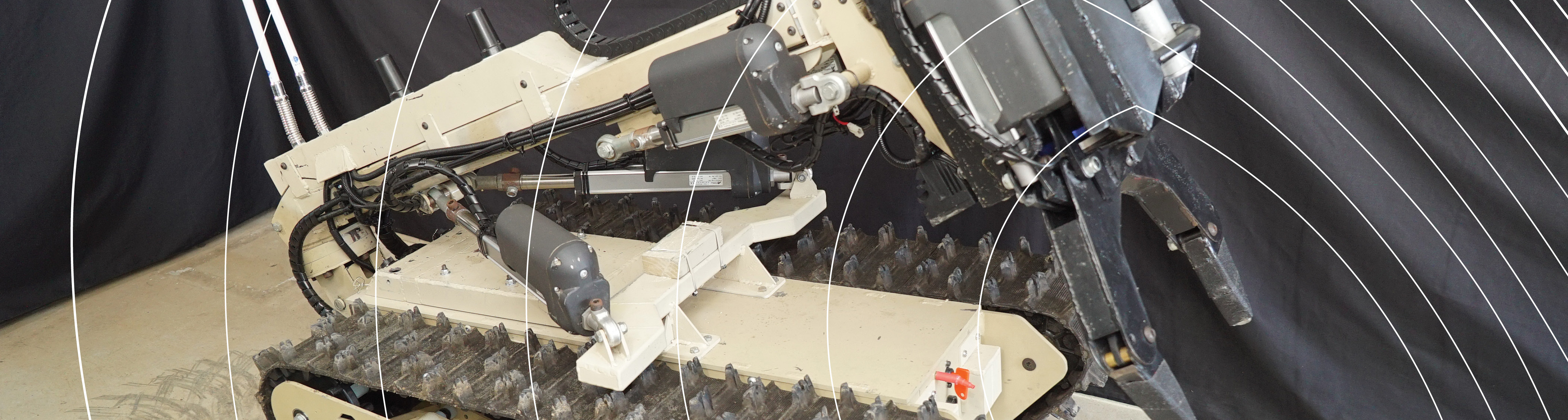
BIA5 Innovation Robotics and customers
BIA5 Pty Ltd is a start-up company that specialises in designing, manufacturing...
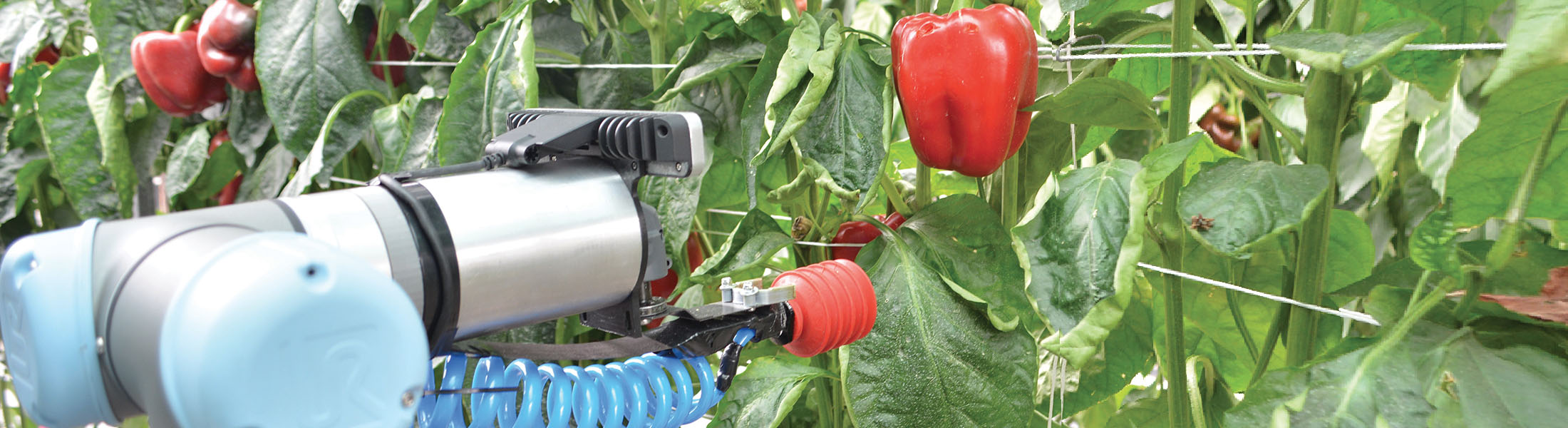
Harvey - the capsicum-picking robot
The horticulture industry in Australia has a gross value of more than $AU8...
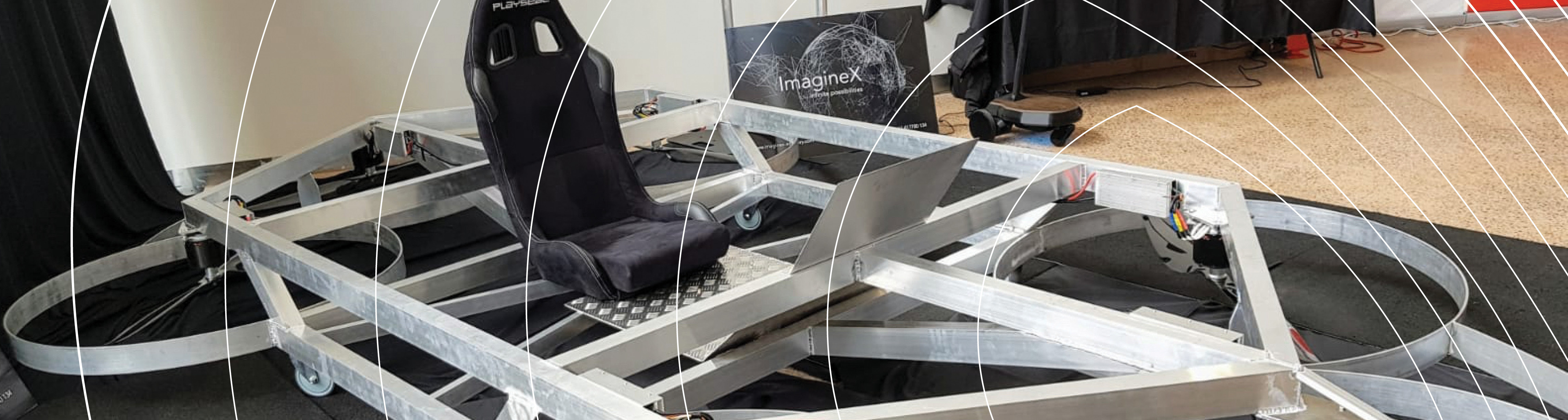
Pegasus Alpha – Flying car
In the back streets of Brisbane, two brothers with a passion for the automotive industry had a feeling that the future is vertical.